In addition to allowing 3D modeling using a scan to BIM process, the point cloud is also an ideal medium for drawing 2D plans.
As explained in our article detailing how 3D scanners work, and how they are used in the building, a point cloud resulting from a 3D survey is a particularly reliable base to be used during the modeling phase.
The use of the point cloud as a modeling medium is very common and relevant in the context of 3D modeling (according to a Scan to BIM process), and it will be just as good to produce 2D plans efficiently.
To do this, it will be necessary to import the point cloud into a software such as Autocad or Revit to use it as a modeling layer. This workflow is commonly referred to as the “scan to plan”.
In this article, we invite you to discover how this method is particularly advantageous for actors wishing to update or produce 2D plans as part of their projects (renovation, studies, layouts, etc.).
Some notions about the point cloud
To get started, it's important to understand what a point cloud is.
A building's point cloud is its 3D digital representation, composed of millions of points defined by x, y, and z coordinates. It results from a 3D survey that may concern several areas of the building depending on the project (interior; exterior; roof; technical plenums; etc.).
This 3D survey is conducted using 3D scanners, and requires the calculation, cleaning and assembly of several clouds captured during the survey intervention to consolidate a global point cloud.
A 3D scanning intervention will take more or less long, depending on the size and specificities of the buildings, but also depending on the type of scanners deployed. As an example, at My Digital Buildings, we deploy scanners that allow buildings to be scanned particularly quickly, with a speed ranging from 3,000 to 12,000 m.2 scanned per day.
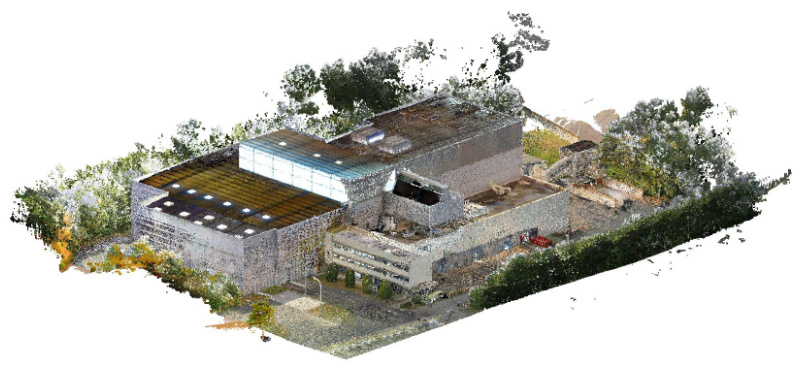
Following this 3D scanning intervention, the clouds generated will remain raw data, requiring to be cleaned, recalibrated and assembled to obtain a global point cloud that can be used during the modeling phase.
To find out more, we invite you to consult our complete article on this subject:” Generating and exploiting a building's point cloud ”, as well as our white paper” The complete scan to BIM guide ”.
The use of the point cloud in the modeling phase
Plans drawn based on sections of the cloud
Once the global point cloud has been generated and controlled, it can be used directly in modeling software, for the production of all types of plans (level plans, facade plans, frame plans, etc.).
For this, horizontal and vertical sections of the cloud will be isolated, and will serve as a layer for the production of the 2D plans requested in software such as AutoCAD or Revit.
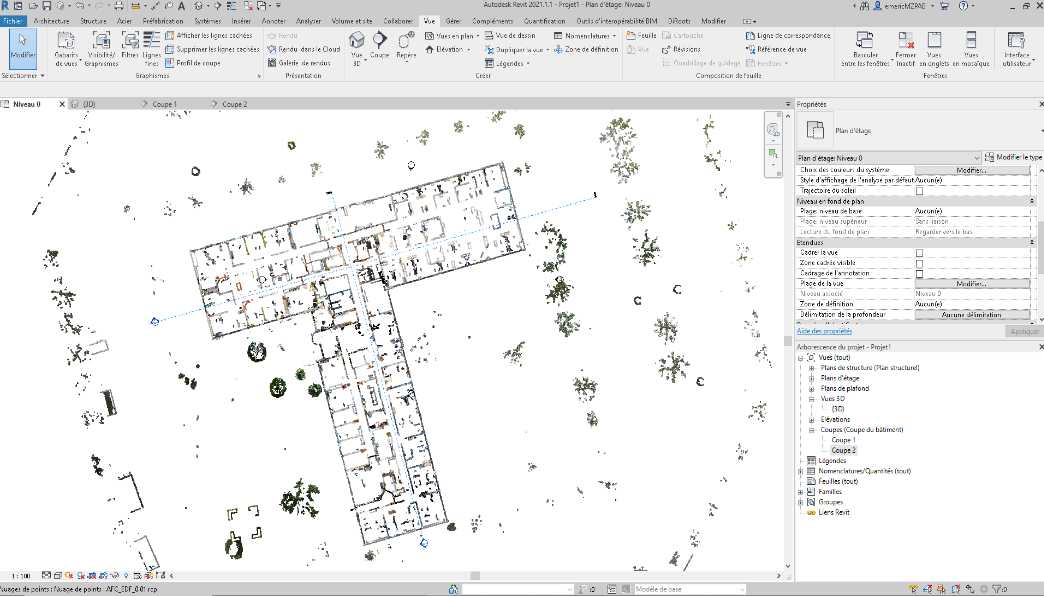
2D plans are then produced based on a precise imprint of reality.
Constant access to the building
While a lack of information on the building creates a risk of errors during the modeling phase, benefiting from a digital footprint of the building will allow for detailed knowledge of it.
Indeed, the point cloud is very suitable for the search for details, so high is its precision and its density of points.
The 2D modeling manager will be able to access this replica of the building at any time through the use of specialized software, or via extensions applicable to modeling software.
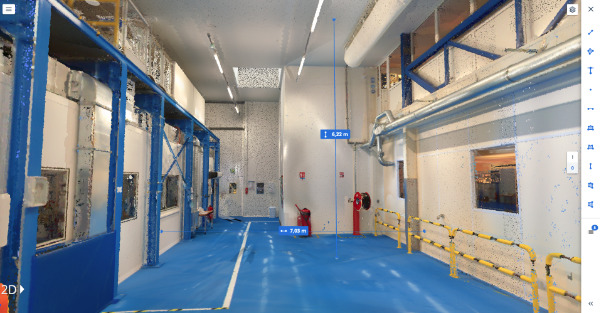
Thus, the modeler will be able to inspect the building in detail, but also benefit from the precision of the point cloud to conduct dimensional checks.
The point cloud: a quality control support
Throughout the modeling, and prior to the final delivery, geometric conformity checks of the plans will be carried out.
During these checks, the point cloud will again be used and compared to the plans to identify the geometric differences between the modeling and the real.
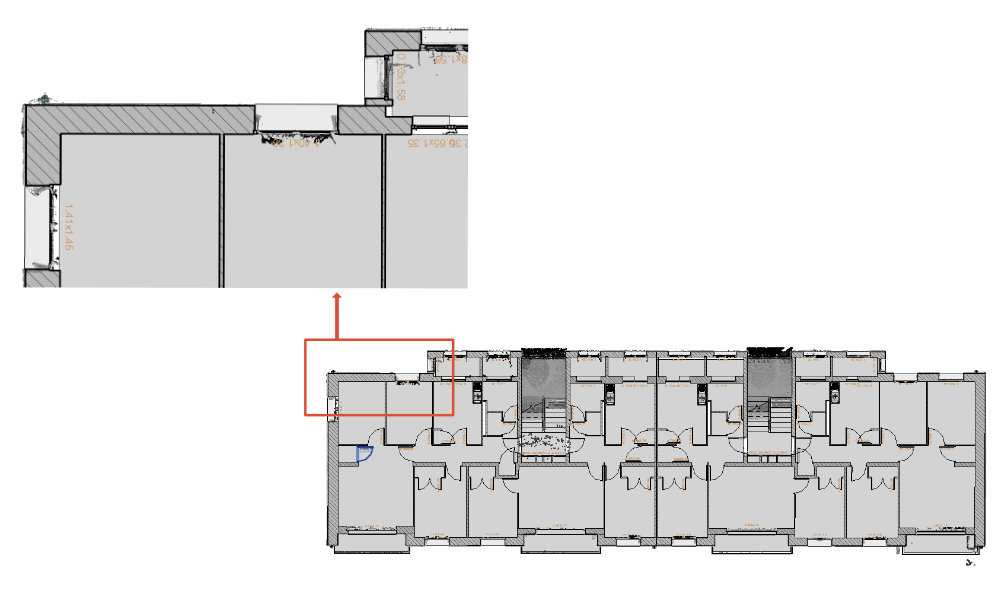
In particular, this method makes it possible to obtain significant modeling accuracy, of plus or minus 1 cm (to plus or minus 2 cm for complex elements) compared to the surveys carried out.
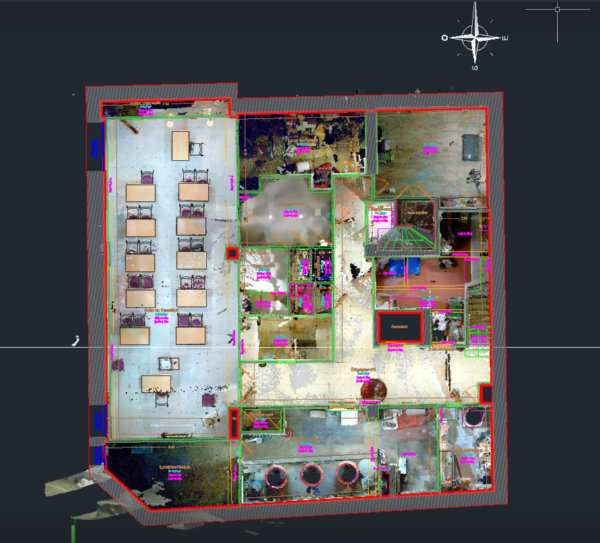
The advantages of “scan to plan”
Accuracy and precision
The point cloud is a particularly precise and representative replica of the geometry of the building. In particular, its use makes it possible to:
- Reduce modeling errors associated with inaccurate or false manual on-site measurements
- Measure details, such as irregular surfaces, curves, and complex architectural elements.
- Conduct quality checks throughout the modeling, and prior to delivery.
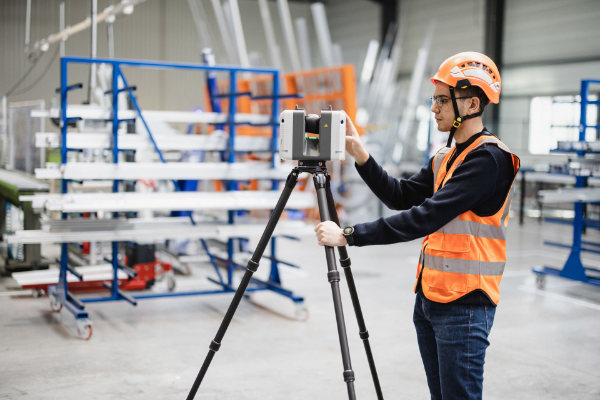
For example, the use of scanners such as the Leica RTC360 will make it possible to generate point clouds with a point density of one point every 3 mm to 10 m, making it possible to identify the finest elements of the environment.
Speed and efficiency
Conducting a survey with a 3D scanner is much faster than a manual survey with a rangefinder, and allows the capture of exhaustive data essential for the production of 2D plans.
As mentioned above, it is possible to survey surfaces of several thousand m2 in just one day, not only indoors, but also outdoors (facades; roofs; land; etc.). Thus, this makes it possible to produce complete plan files including all the structural and architectural elements necessary for the project.
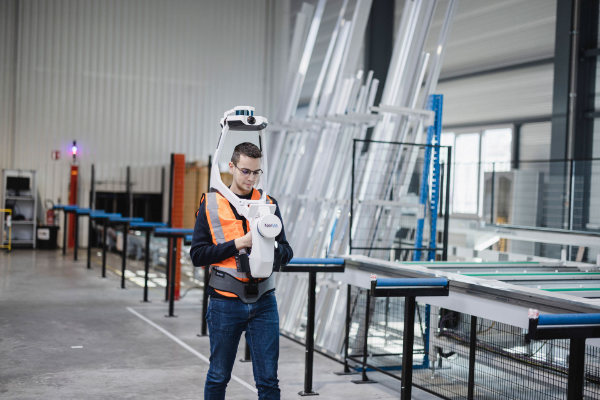
For example, the use of mobile scanners (such as the NavVis VLX scanner above), making it possible to digitize an environment while in motion, gives a survey capacity of up to 15,000 or even 20,000 m2 in very open areas.
By reducing survey time, it is important to note that the disturbance will also be reduced for building occupants.
Profitability and productivity
Finally, some actors (architects; design offices; etc.) will be able to focus on their core business, while the 3D survey and drawing up will be carried out by specialized and well-equipped actors.
This gain in productivity is not negligible, especially since the deadlines for producing plans will be reduced!