Context
Dassault Systèmes, one of the largest software companies in the world, is well known in the industry for its solutions around 3D design, 3D digital modeling and solutions for product lifecycle management (PLM). Its main software (Catia, SolidWorks, Delmia, etc.) are references in the field.
In 2019, Dassault Systèmes acquired Medidata Solutions for $5.8 billion and took a significant step forward in the health sector by buying this American company specializing in medical software.
In industry, one of the scourges that costs manufacturers around 8% of their payroll every year is MSDs (Musculoskeletal Disorders). Indeed, each TMS generates direct costs, days of absence, recruitment and training (often temporary workers), reduced quality and other disruptions. The challenge is therefore major and Dassault Systèmes decided to tackle it by developing a solution designed to diagnose the risk of exposure to these MSDs.
The MyHealth @Work offer
Digitization and 3D modeling of workstations
Dassault Systèmes' offer allows manufacturers to carry out the broadest possible biomechanical audit of the risk of exposure of their employees to potential MSDs. This audit is carried out in two stages.
The first step consists in retrieving data to analyze the working environment of operators in their daily lives. This is where My Digital Buildings intervenes. The objective is to digitize in 3D the workstations that will be studied. To do so, a dynamic 3D scanner is used to simultaneously capture 3D data and 360° photos. The 3D data is assembled in the form of a point cloud with an accuracy of less than one centimeter. This point cloud, made up of thousands of points, all with precise coordinates in space, makes it possible to reconstruct a true footprint of the environment. Based on this cloud, the workstations are modelled in 3D in the software CATIA from Dassault Systèmes.
Simulation and evaluation
In the second stage, the gestures made by the operators on the workstations are studied and integrated into the DELMIA software to be simulated by 3D models. These simulations integrate parameters such as size, morphology, the weight of the objects manipulated or the frequency of operations and analyze the risk level of each posture.

After simulations and ergonomic analyses, each workstation is evaluated using an MSD exposure index of between 0 and 5. The customer can access all data on the Dassault Systèmes' 3DExperience platform. This takes up the virtual tour of the factory and allows you to travel, to the stations studied, in 360° photos to confront the virtual 3D models with reality. He can then visualize the TMS risk exposure index by workstation, then he can also detail the result of the analysis carried out on each work sequence according to morphologies and to very quickly visualize those that present a risk.
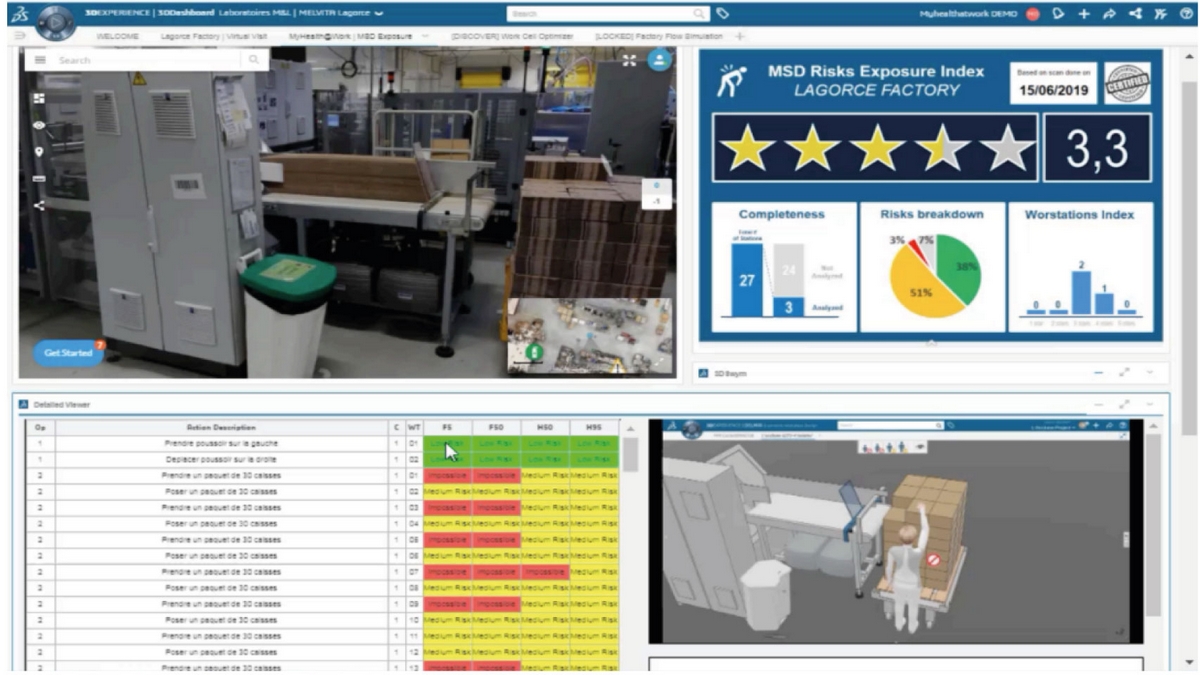
A pilot project with the L'OCCITANE Group
The project of the L'OCCITANE Group and its French subsidiary
For this pilot project in the field of TMS risk prevention, Les “Laboratoires M&L”, a French subsidiary of the L'OCCITANE Group, was seduced by the added value proposition offered by the prospects of the project led by Dassault Systèmes.
For the past ten years, the group has been committed to a preventive approach aimed at improving ergonomics at workstations. At its production site based in Ardèche (Lagorce), the approach has been carried out for all these years by a small team that has acquired expertise in the subject. A team that pragmatically leads and supports this transformation of the workstations of all the factory's industrial activities. This confirms that conducting this audit concerning MSDs internally and defining areas for improvement requires months or even years, even for people who are experienced in these analyses, in the automotive and household appliances industries.
Another important point, it is clear that having teams equipped with these skills that provide the time for analysis and the implementation of corrective solutions is an opportunity. This is a chance that many businesses cannot afford.
From the beginning, the L'OCCITANE group identified the potential that this new approach could offer. Moreover, committed to the digital twin experience on the one hand and a strong partnership with Dassault Systèmes, it was quite natural that they would together lay the foundations for this project and give it the impetus it deserves.
Thus, as explained in the paragraph specifying the MyHealth @WORK offer, each workstation was modelled on the basis of the point cloud as input data for the Dassault Systèmes teams. The data associated with the operating procedures are then added. Everything went through the filter of simulations, calculations and expertise of the Dassault Systèmes teams to deliver an index of risk of exposure to MSDs. The mapping of the risk level of each station thus provided makes it possible to target prevention activities where the risk is the highest. It is also a medium for exchange and communication between the various internal and external actors concerned with this problem.
12.000㎡ recorded in one day of 3D scanning
As a Dassault Systèmes partner, we therefore intervened to identify one of the L'OCCITANE Group's production sites and provide a complete building point cloud.
This 12,000m² industrial environment was identified in a big day of digitization with a Mobile scanner NavVis M6. The identified point cloud was the ideal support for fine modeling of production lines.