The project
As part of a development project, we identified and modelled a finishing workshop at an ALSTOM TRANSPORT production site. Located in Belfort, it is in this building that the engines of the first trains of the TGV of the future, called TGV-M, are manufactured!
The objective of this operation was to provide the building operator with a spatial reference system allowing him to optimize the installations that will be made to the production lines. In addition, the digital twin of the building will reinforce the transition to the industry of the future that is taking place on this site, which is particularly rooted in innovation, especially in terms of production.
The solution provided
Produced on the basis of a single capture, the BIM model and the building's “Google Street View” digital twin, were thus the two deliverables selected by Alstom. The first serving as a modular geometric frame of reference, and the second as a photorealistic, collaborative and accessible alternative from the web (thus does not require any specific equipment or operating software).
The production workshop extends over a single level composed of a central circulation aisle, surrounded by spaces particularly congested by metal walkways, production lines, engines and production equipment. Moreover, these two very distinct configurations were decisive elements in the selection of scanning solutions.
Despite the congestion and the surface of the building, the survey was carried out in only 7 hours thanks to the combination of several 3D laser scanner technologies. Below are more details about this operation and the final exploitation of the two digital twins delivered.
A multi-technological survey protocol
In order to carry out this intervention as soon as possible, while capturing data with optimal precision concerning their future operations, we opted for a survey combining different 3D scanners.
Given the specificities of the building and the specifications, we first chose to exploit the mobility and capture capacity of the NavVis M6 scanner on the ground floor of the building and the main traffic aisle. Thus, we were able to digitize this entire area very quickly, while scanning the surroundings of nearby congested areas.
At the same time, we completed the survey with a Faro X130 static scanner allowing access to the least accessible parts (traffic aisles and high-rise footbridges) and to benefit from greater capture accuracy on components subject to more detailed modeling. In order to assemble the various data sets captured, we used realignment spheres and GCPs that were placed on the ground.
Opt for a 3D survey of the building combining several 3D scanning solutions has thus allowed us to make the most of each of them and to optimize our intervention.
The exploitation of digital twins
The BIM digital model
A “Scan to BIM” project
The BIM digital model delivered is the result of a “scan to BIM” process, i.e. a 3D modeling of the building based on the point cloud captured during our intervention on site. We'll discuss the benefits of this method in more detail later in the article. If you want to know more about the different stages that make it up, we invite you to read our article on Scan to BIM.
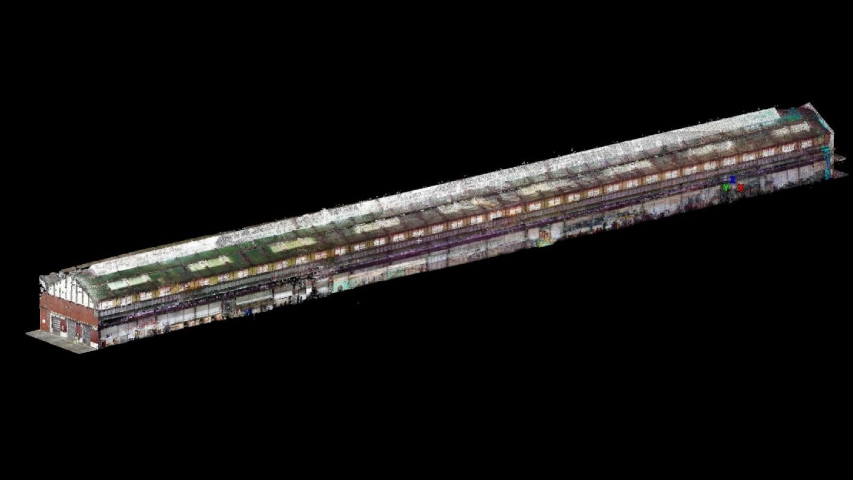
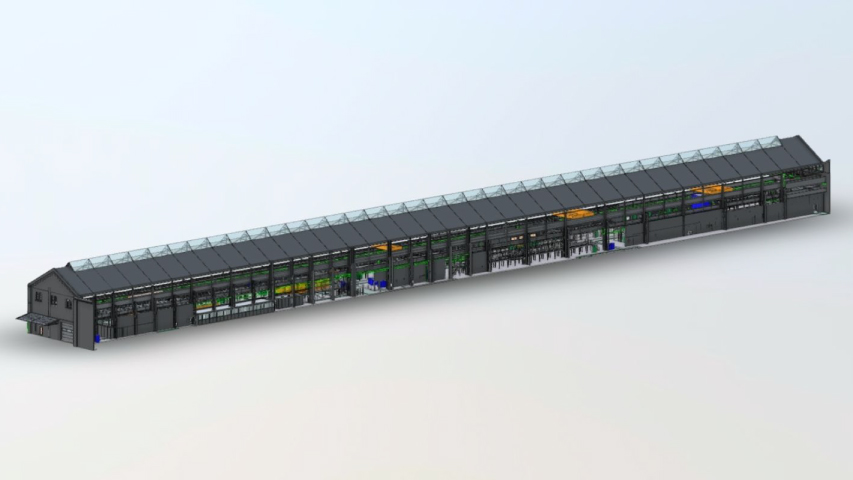
An adapted level of geometric detail
In order to optimize the costs and delivery times of the model, while meeting the needs of the customer, each area of the building was modeled at a precise level of detail.
Thus, the structures and networks (electricity, plumbing, compressed air, etc.) were modelled at LOD 300, since they were heavily involved in the planned arrangements. This also made it possible to quickly detect installation conflicts between components with similarities, such as gateways and power supplies for example.
Conversely, the structure and framework of the building were modelled with LOD 200, since they are not involved in the simulations of developments envisaged inside the building.
Finally, the machines were represented in the form of simple “bounding boxes” (rectangular parallelepipeds representing a volume). These will eventually be replaced by the 3D objects of each machine model that Alstom has, in the Catia software.
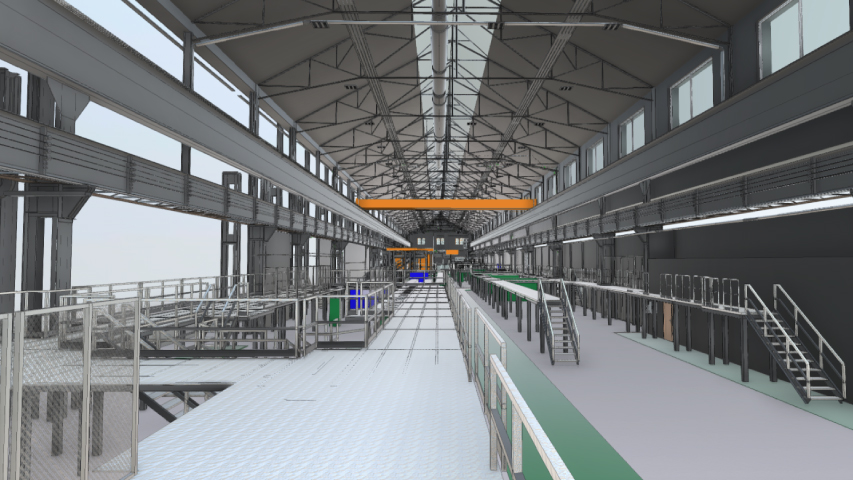
The digital twin like “Google Street View”
In order to offer a digital twin that can be used by general services and maintenance teams, we also delivered a digital twin in the “Google Street View” style of the building. This is similar to a collaborative virtual tour, created based on the point cloud and panoramic photos systematically captured by our scanning solutions.
The advantage of this alternative to the BIM model lies in its accessibility. Indeed, this digital twin is accessible from our web platform, and therefore does not require any specific software or equipment to be exploited. On the contrary, the collaborative functionalities of our platform (taking measurements, surfaces, adding and editing georeferenced points of interest, sharing views, etc.) allow it to be easily exploited.
Thus, all building actors (maintainers, facility managers, sales or marketing teams, etc.) benefit from this spatial framework opening up to a multitude of use cases.
The advantages of the scan to BIM process
By modeling based on the captured point cloud, we were able to benefit from a 3D footprint representative of the building and what is inside (machines, structures, networks, etc.). Taking advantage of this 3D layer on which to base ourselves allows us to be more precise during the modeling phase, but also faster.
Based on this 3D footprint, we deliver a model qualified as “As-Built” (as built), which can be perfectly used in the Operational Maintenance Management phase and can be integrated into a future digital DOE (File of Executed Works).
Moreover, based on the point cloud, there is no doubt about the compliance of the data. This is not systematic when modeling on the basis of 2D plans, the maintenance of which sometimes involves many questions that only site visits can answer.
Finally, as explained above, we also delivered a digital twin in the “Google Street View” style of the building. This was a real modeling aid, since it allowed the modellers to virtually navigate the building from our web platform. Thus, he can perform remote checks and have access to contextualized information, which was a valuable aid in network modeling in particular.
Go further
Scan to BIM: 12 steps to bring an existing building into BIM